HOW IT WORKS
FLUID SAVER CONTAINER (Patent Pending)
- As the CNC machine runs, the chip conveyor delivers the chips into a chip bin or drum that has the capability to allow the cutting fluid to drain out of the bottom or side proactively. (Refer to Drum & Dolly/Drum filter images below.)
- As the cutting fluid percolates through the chips to the bottom, the cutting fluid continuously drains into the Fluid Saver container through the mesh screen.
- When the cutting fluid level reaches a predetermined amount, a switch is automatically triggered, a pump then recycles it back into the CNC machine's cutting fluid reservoir.
- This process continues automatically, without human supervision or interaction, during the entire run cycle(s).
- Once the chip bin is full, it can be moved to another location to allow it to continue to drain before recycling. Note: The secondary draining location can be either somewhere else in the facility or rotated around to the other side of the existing Fluid Saver container.
- An empty chip bin can then be rolled into place underneath the chip conveyor and placed over the Fluid Saver container. With the valve opened, the process repeats itself.
DRUM & DOLLY (Patent Pending)
- Our patent pending drum dolly system is designed and tested to function together. The filter and draining components are designed to allow the cutting fluid to drain proactively while the drum is resting within the dolly. When the drum is removed from the dolly, the filter will automatically seal, preventing the cutting fluid from dripping onto the shop floor.
- When the drum is full of chips, the valve is closed and moved to a secondary location to allow the cutting fluid to continue to drain.
- Once the drum is completely drained, empty the chips as necessary. When removed from the dolly, the filter mechanism automatically seals, preventing any cutting fluid from dripping onto the floor.
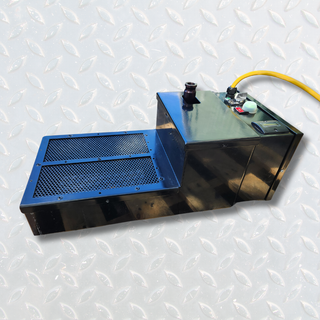
The Fluid Saver
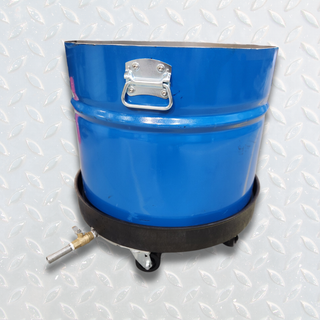
Drum & Dolly
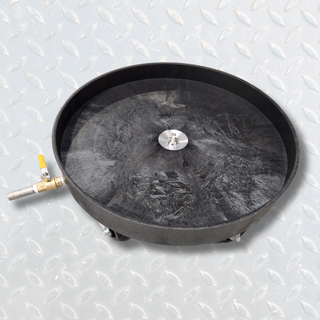
Dolly
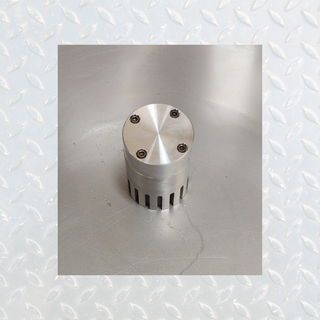
Drum Filter
THOUSANDS IN POTENTIAL SAVINGS
Depending upon the frequency of the machine operations, cutting fluid costs per gallon, etc., the ROI of the Fluid Saver system could be as little as 3–4 weeks per machine/system. In addition to the ROI of proactively reclaiming cutting fluid, recycling companies may provide higher scrap prices per lb. Further, our experiences have demonstrated that if the scrap bin is allowed to “sit” offline and continue to drain, an additional 1-3 gallons can be reclaimed.
The need to postprocess the chips through a centrifuge or other methods may be negated and/or significantly reduced, thus saving additional costs and time.
The following numbers are based on our own use of the Fluid Saver:
In addition to the savings above, use of the Fluid Saver greatly reduces the need for a manned operation, thus saving time and money. By eliminating potential spills and messes, we're able to have continuous production and little to no downtime.
ABOUT THE Designers
FLUID SAVER
Innovating Since 1997
Fluid Saver is a locally owned company from Ogden, UT. We have proudly been providing manufacturing and engineering services nationwide since 1997. Our company is owned and operated by three brothers, with a combined experience of 89 years. They strive to excel in their craft every day.
The Fluid Saver and its corresponding products are just a few of our patent-pending innovative ideas. We have designed, developed, and tested these products internally to increase efficiencies and decrease costs, resulting in saving thousands of dollars each year, directly increasing our customers bottom line.